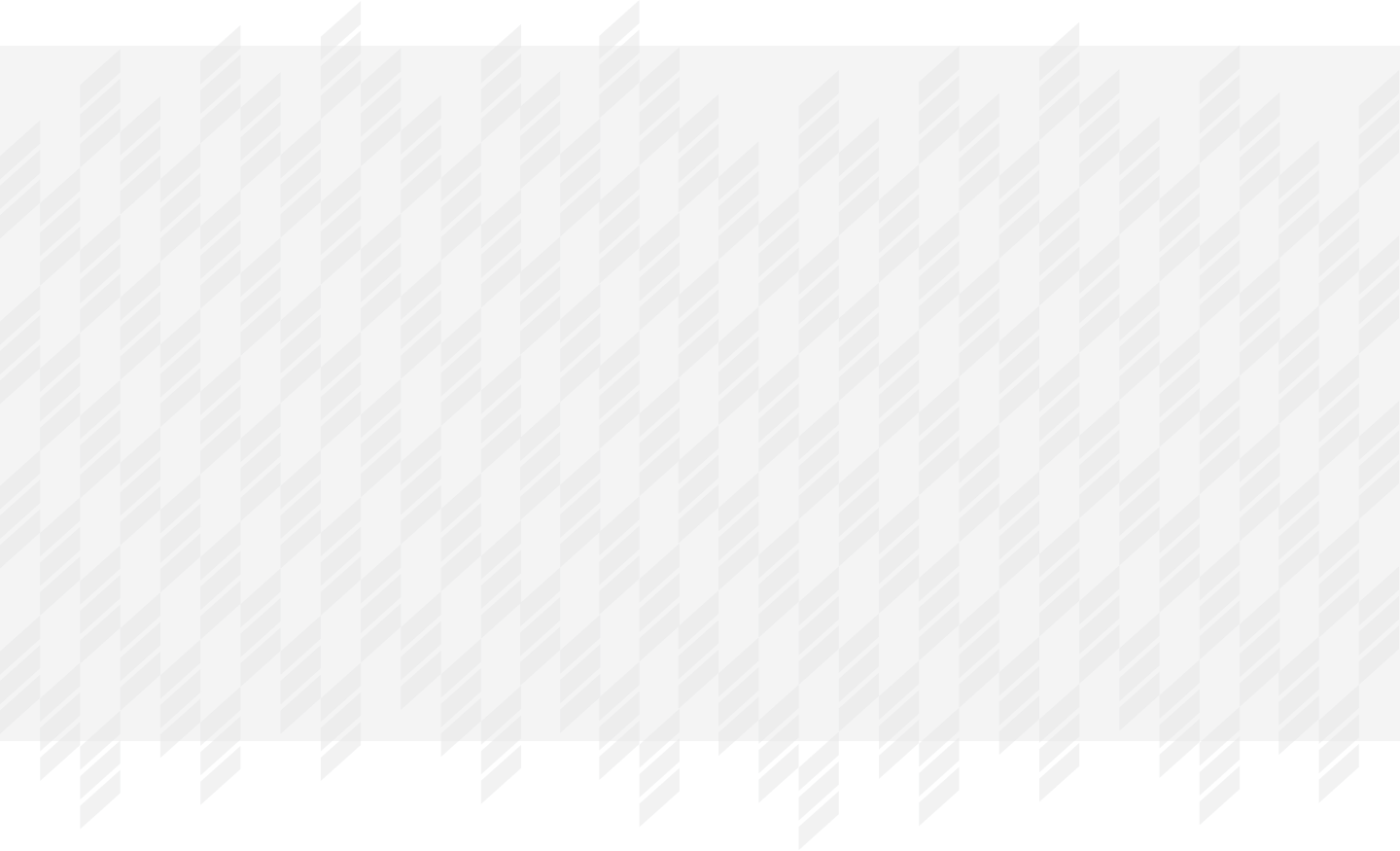
Get the Brochure
Download BrochureProducts / Vapor Intrusion Barriers
Composite System
Geo-Seal composite systems provide triple layer vapor intrusion mitigation protection and are available in a variety of thicknesses. Download Brochure
Sheet Membranes
Geo-Seal EV40s and Geo-Seal EV20 provide single sheet membrane vapor intrusion protection coupled with Geo-Seal CORE spray membrane for superior constructability versus taped membranes. Download Brochure
Epoxy Coatings
A chemically resistant coating can mitigate the vapor intrusion risk and provide little disruption to building occupants for existing structures with contaminant vapor intrusion concerns. Download Brochure
Venting Systems
Low-profile trenchless venting aids in preventing contaminant vapors from building up under the building foundation. Download Brochure