There are many benefits to developing brownfield sites, and vacant gas stations fall under that category. According to the EPA, of the estimated 450,000 brownfield sites in the U.S., it is believed that approximately half of these are impacted by leaked petroleum from underground storage tanks (USTs) at former gas stations.
And the number of disused gas stations is predicted to go up: Demand for more gas stations is decreasing, according to a Crosscut article on this topic. Lower profits, higher urban land prices and the demand for more fuel-efficient cars leads to stations being left vacant.
These former gas stations are frequently located on opportune corner locations, on flat land, and developers are moving in to turn the spaces into strategically-located residential or mixed use structures. Before these sites are ready for a new build, however, they must be assessed, treated, and cleaned up - and the level of cleanup can vary in complexity depending on the site’s end use, be it a parking garage or residential building, according to the EPA.
To aid in the cleanup process, a vapor intrusion mitigation may need to be used as site clean-up may still be active after building construction or to mitigate low levels of remaining contamination. And this is where EPRO steps in. We have been involved in several projects built on former gas station sites because our products present the ideal solution to prevent vapor intrusion and also groundwater infiltration:
1 Florida Ave NE in Washington DC
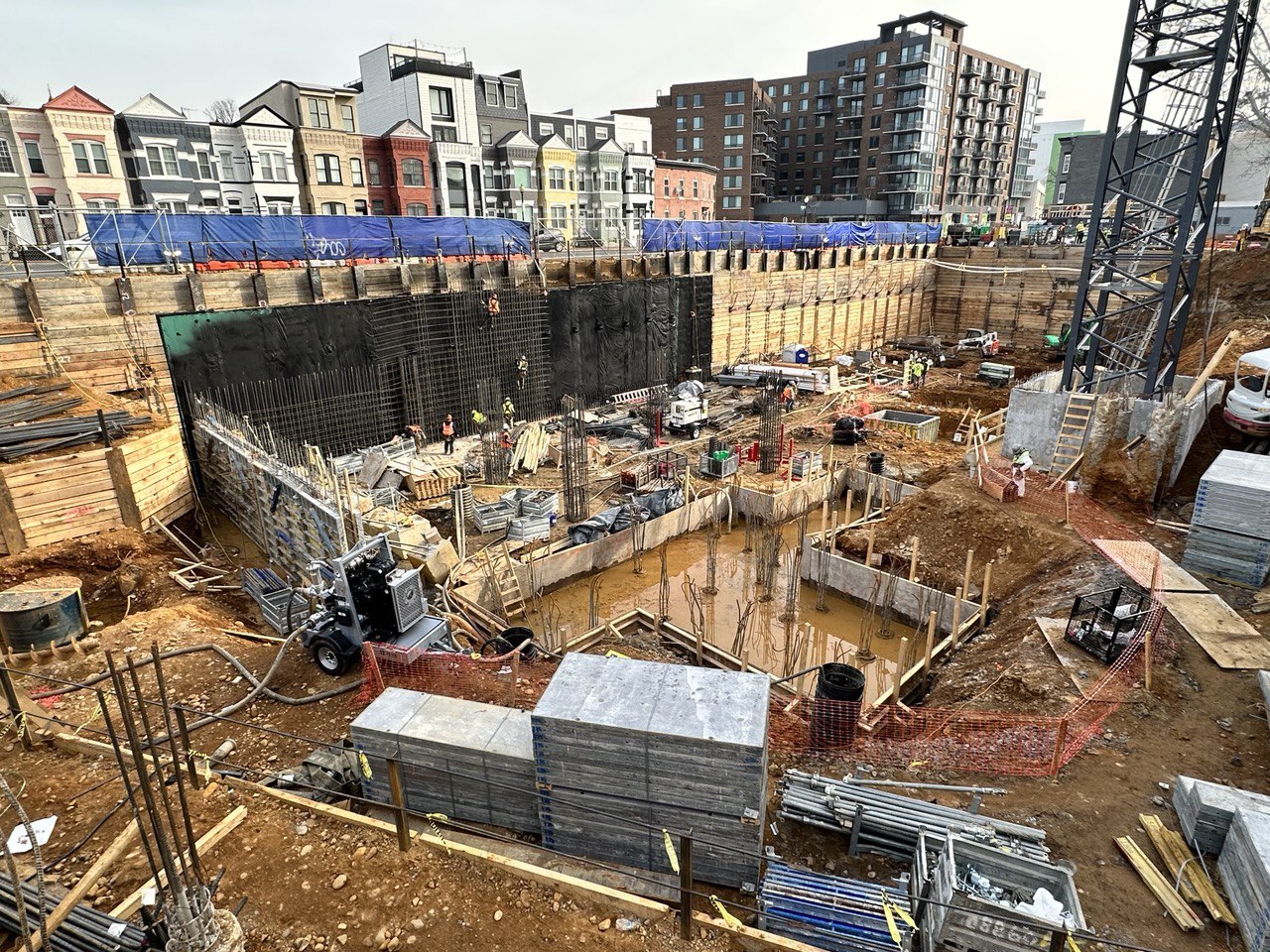
The 1 Florida Ave NE condo project is currently under construction. Plans call for 388 apartments which will be situated on the site of a former Exxon gas station at the corner of North Capitol St and Florida Ave NE.
At this site, it transpired that one of the underground storage tanks had leaked into the soil, causing a complete exposure pathway from the groundwater to the indoor air.
EPRO stepped in with the right products and expertise to advise the team on the best way to protect the site. A total of 47,000 square feet of product was applied: Geo-Seal EV40s with passive low-profile venting for vapor mitigation; e.base, e.spray, Geo-Seal Bond B at the elevator pits; 12,500 square feet of E.Proformance Slip Sheet at shoring for the blindside walls, and 7,500 square feet of the post-applied E.Proformance Wall system for the double-formed walls.
West Jefferson Blvd, Los Angeles, CA
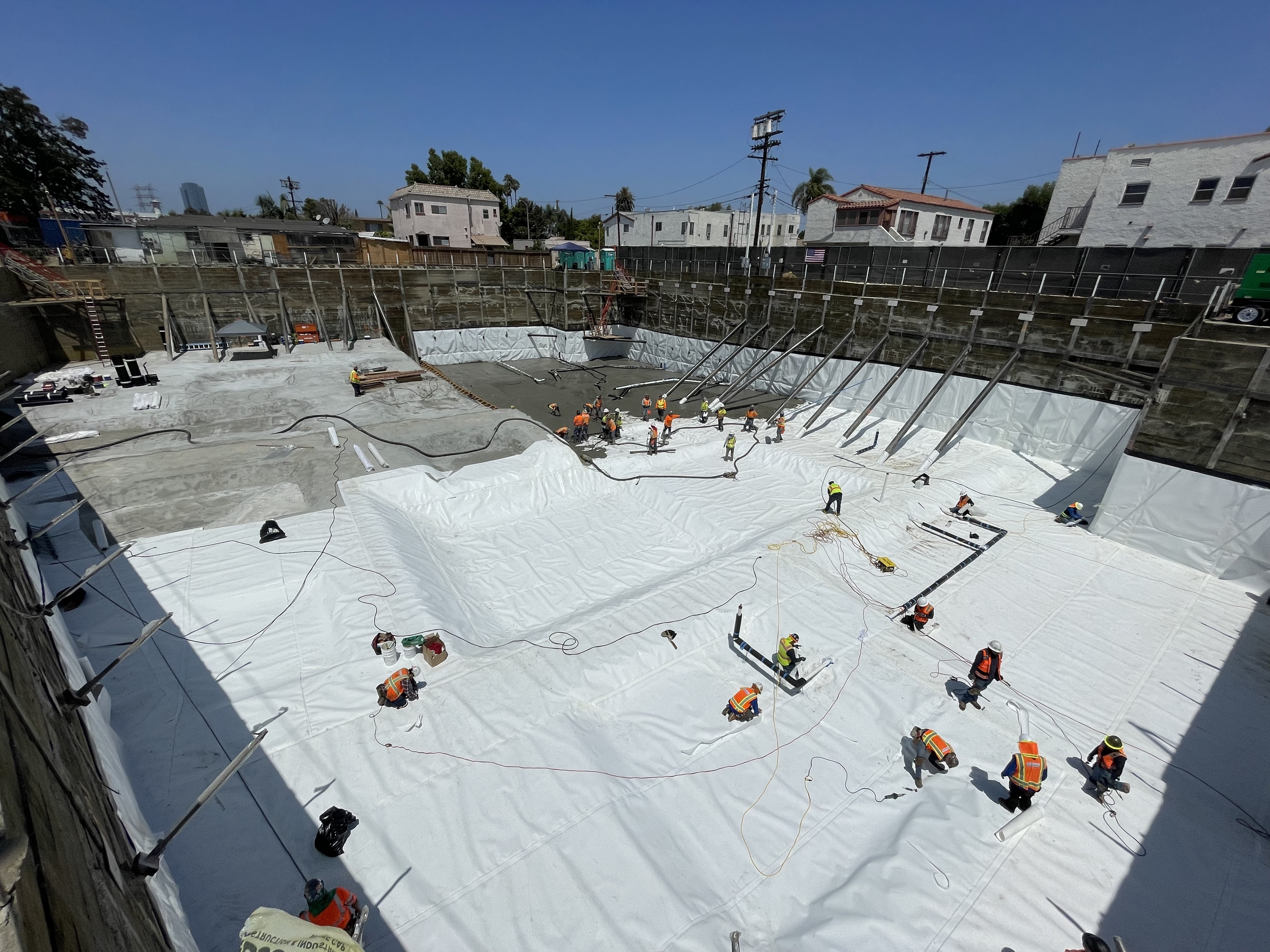
A new office development located on the 5200 block of W. Jefferson Blvd in Los Angeles is situated on a former gas station and car service facility.
The bottom of the building foundation is right above the water table, and there were vapor intrusion concerns due to the site’s history. These conditions required a preventative measure, so the specified product had to mitigate both potential water intrusion and vapor intrusion.
EPRO’s PreTak HW was selected to protect against water ingress and the environmentally impacted soil. The specification called for a continuous full bathtub application, meaning the system needed to run uninterrupted from under the slab and up the vertical blindside walls. PreTak HW’s ease of application, tested performance, and overall cost effectiveness were the reasons the waterproofing consultant and general contractor decided PreTak was a great solution for the site.
Roystone Apartments, Seattle, WA
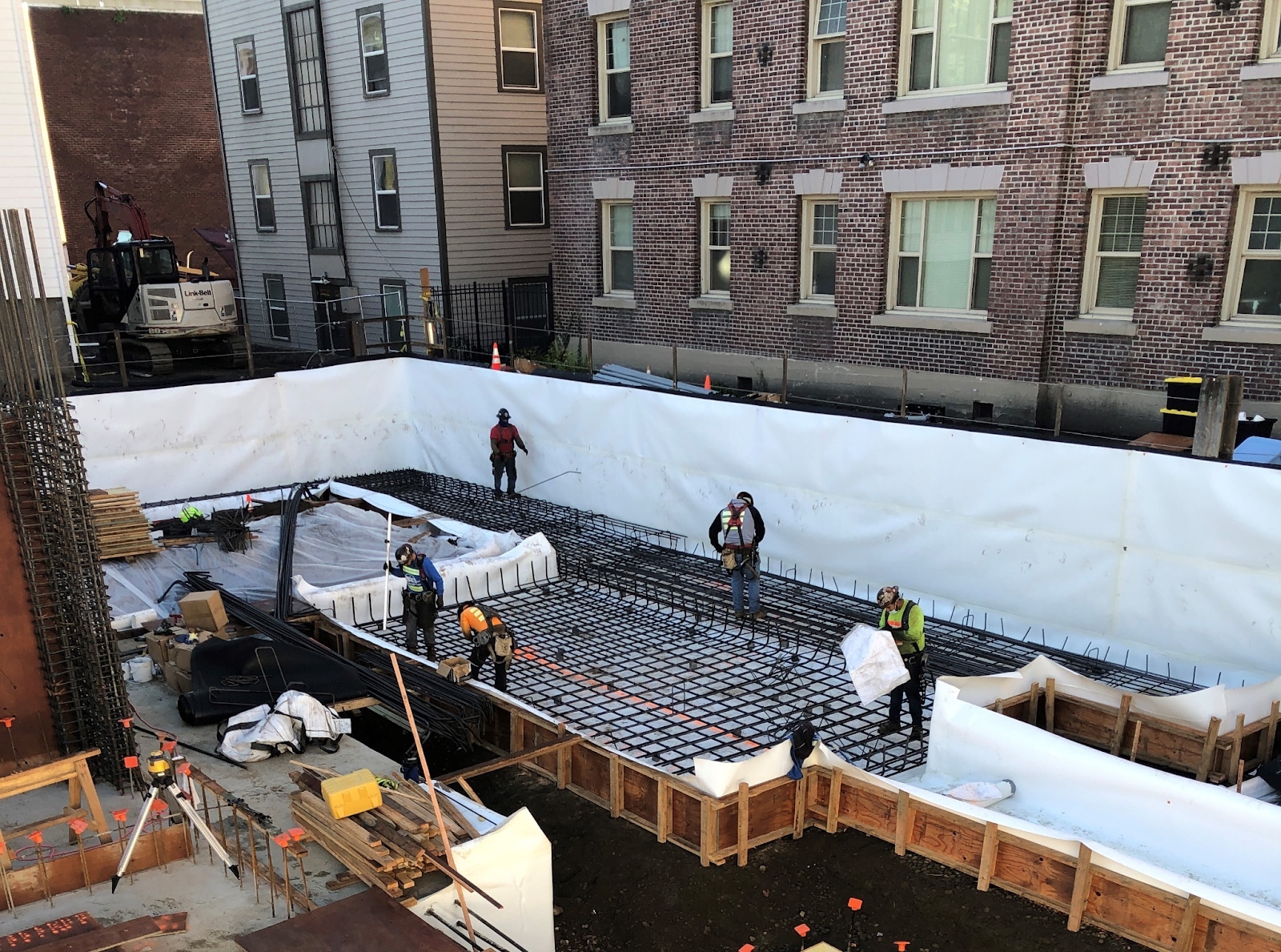
Here, a Texaco gas station operated on the land from 1923 to 1993. There was also shallow groundwater present in addition to vapors from the former gas station, and the project design team was tasked with the selection of an appropriate waterproofing and contaminant vapor intrusion system.
EPRO’s PreTak membrane was determined to bet the ideal solution and was installed at all underslab locations directly over compacted fill and vertically against the soldier pile lagging support of excavation (blindside waterproofing). The blindside assembly consisted of EPRO’s e.drain drainage composite with embedded filter fabric against soldier pile lagging with PreTak mechanically fastened to the lagging.
This fully adhered waterproofing and contaminant vapor intrusion barrier system effectively eliminates the potential for lateral water migration between the installed membrane and concrete substrate while effectively protecting the structure from residual subsurface contamination.