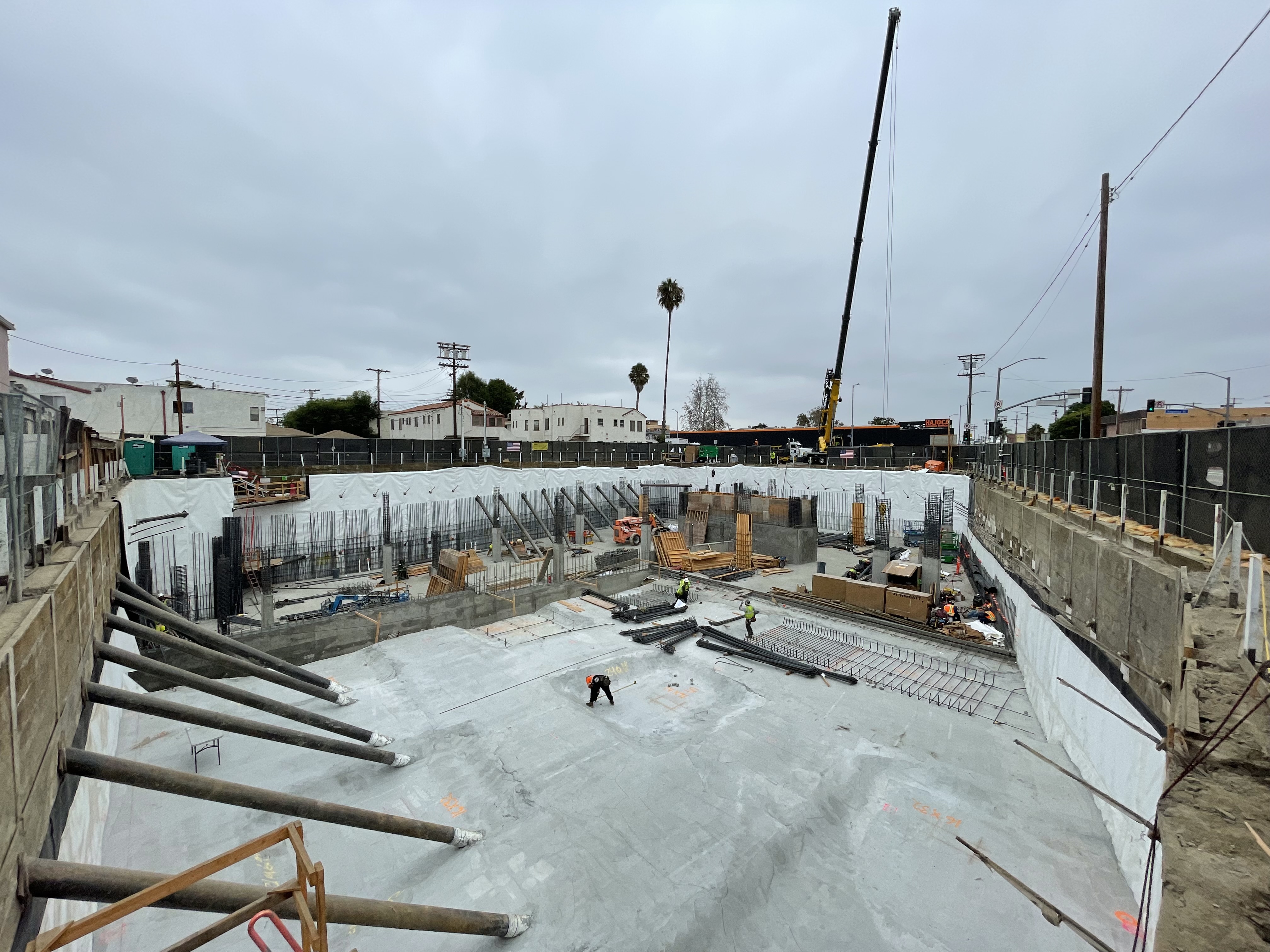
The bottom of the building foundation is situated right above the water table, and there were vapor intrusion concerns due to the site’s history as a gas station. These conditions required a preventative measure, so the specified product had to mitigate both potential water intrusion and vapor intrusion. Due to site access restrictions for heavy equipment, the material also had to be light enough for laborers and easy to stage for installation.
EPRO’s PreTak HW, a HDPE self-adhesive pre-applied waterproofing membrane with seams designed to be heat weld capable, was selected to protect against water ingress and the environmentally impacted soil. The specification called for a continuous full bathtub application, meaning the system needed to run uninterrupted from under the slab and up the vertical blindside walls. PreTak HW’s ease of application, tested performance, and overall cost effectiveness were the reasons the waterproofing consultant and general contractor decided PreTak was a great solution for the site.
“One of the benefits of the product was that it was hot-air welded, so this definitely saved us some time on site,” says Kevin Burpee, Senior Superintendent, Suffolk Construction, the general contractor.
“The mat foundation system had thickened areas so we could not utilize equipment in the hole but the size of rolls were manageable by hand. This meant that the only equipment required to lower them into the 40’ deep excavation stayed on the street. On a site like this, it was key to maneuvering the material and getting it applied quickly and easily.”
Not only was the product extremely easy to work with, but the EPRO team went above and beyond to ensure everything ran smoothly.
“We started the project off with submittals and pre-construction meetings with all trades from rebar, electrical, and formwork to show the properties of the product and the items that would require detail work from the waterproofer. Each day we had an inspection, and the EPRO team was here at least once a week,” Burpee says.
“The entire EPRO team was responsive, and worked towards solutions for challenges or specific field conditions we encountered,” he adds. “They conducted frequent site visits and were very active in the project, which helped things run smoothly and on schedule.”
The project architect is Abramson Architects, the general contractor is Suffolk Construction, and the EPRO Installer is Mark Beamish Waterproofing, Inc. The project is currently under construction and slated to be completed in June of 2023.