Collection 14, located in Washington, D.C.’s 14th Street Corridor, is one of the most significant landmark redevelopment projects. The block-long redevelopment required the purchase of multiple addresses, including the former Martha’s Table headquarters, to create a mixed-use project featuring residential, retail, office, and events & art space.
Collection 14 integrates and preserves historic facades and incorporates historical structural elements into the new building, which has an inviting streetscape that embraces positive change in the neighborhood.
The project consists of a one-story below-grade basement that extends approximately 22-feet below ground surface with a foundation using zero lot line construction. A complex Support of Excavation (SOE) system utilized soldier pile lagging with temporary raker supports and underpinning to support existing facades and an existing structure along the southern edge of the excavation.
The SOE system also included a back-lagging condition that consisted of installing timber laggings on the backside of the soldier piles. The back-lagging condition, rakers and underpinning required custom waterproof detailing to the SOE system to ensure watertight protection.
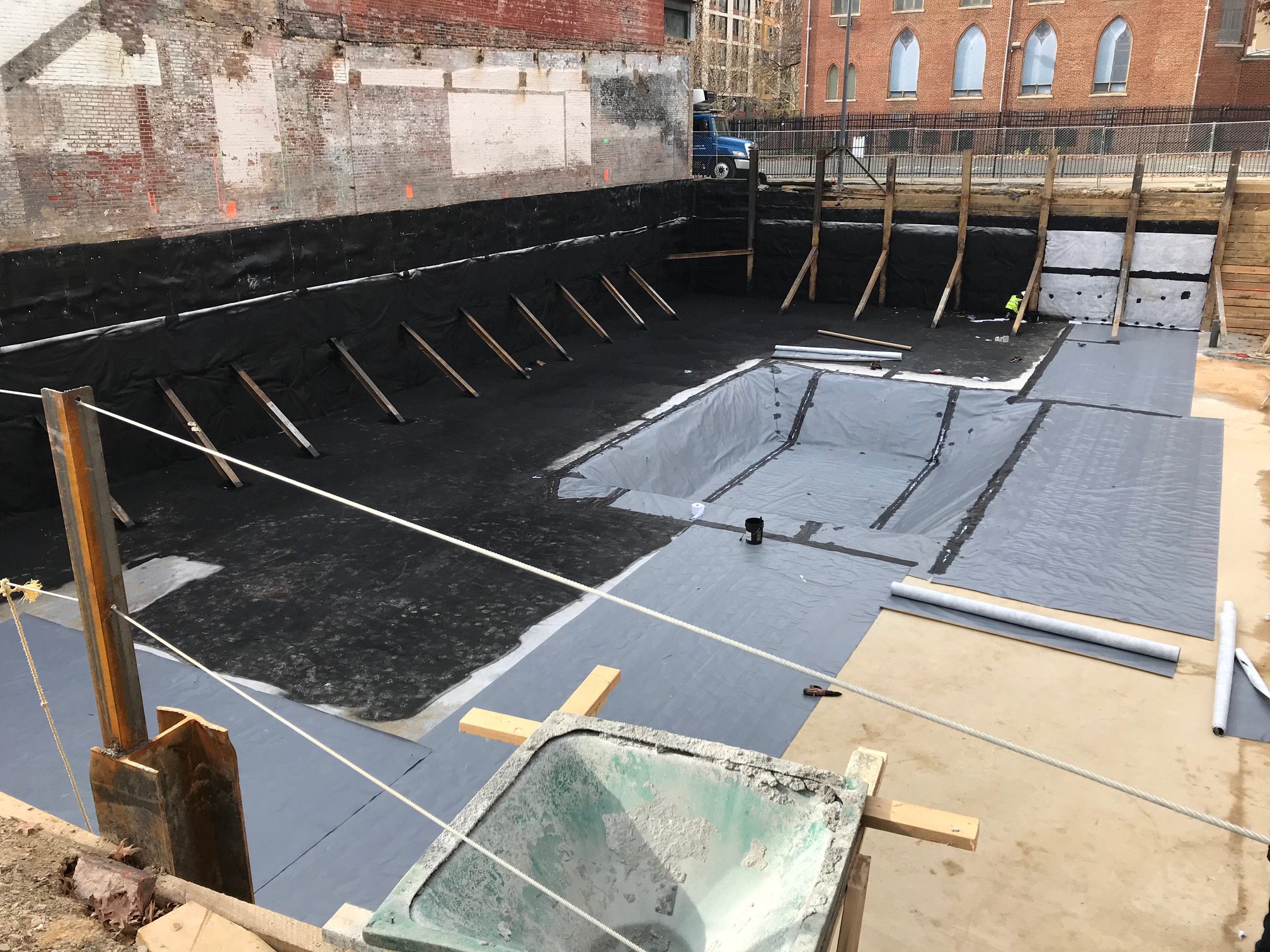
The foundation included a continuous, thickened mat slab that could accumulate groundwater under the foundation. A fully encapsulated, bathtub waterproofing system was required to protect the foundation from the buildup of hydrostatic pressure and groundwater infiltration.
Additionally, the system had to serve as a contaminant barrier to further protect the subsurface building envelope against residual contamination from a former gas station and former adjacent dry cleaner.
EPRO confidently addressed the many challenging conditions: Over 65,000 square feet of Geo-Seal® 100 was installed with 15,000 square feet of Geo-Seal applied blindside on shoring foundation walls and 40,000 square feet of Geo-Seal applied under the reinforced mat slab. The project was locally supported by EPRO’s representative firm, Conners Group, and field installation training was provided to Potomac Waterproofing.
The Washington, D.C. Department of Energy and Environment (DOEE) reviewed and approved EPRO’s Geo-Seal 100 System to protect the structure from water and environmental contamination.
“In addition to being competitively priced and less labor-consuming than other systems, the Geo-Seal system is very robust. As an installer, we have peace of mind that the system is not prone to damage as we are less concerned with damage control after the barrier has been installed. Most failures in waterproofing occur from damage to the membrane after the installation has occurred,” says Danny Santos, Vice President of Potomac Waterproofing based in Manassas Park, VA, an E.Assurance certified EPRO applicator.
Geo-Seal 100 is a 96-mil field-installed composite membrane system consisting of a base 18-mil HDPE geomembrane (Geo-Seal® BASE), 60-mils of polymer modified asphalt (Geo-Seal® CORE), and a protective 18- mil HDPE geomembrane (Geo-Seal® BOND). The Geo-Seal system provides an ideal blend of durability, constructability, and chemical resistance, and the system has been rigorously tested to determine its ability to protect from environmental contamination. Geo-Seal 100 was selected over a 46-mil HDPE membrane with pressure-sensitive adhesive.
EPRO provided a ten-year Labor and Material warranty, which is a standard offering in their E.Series warranty program. EPRO offers a unique warranty offering, as warranties are available for site contamination in addition to waterproofing.
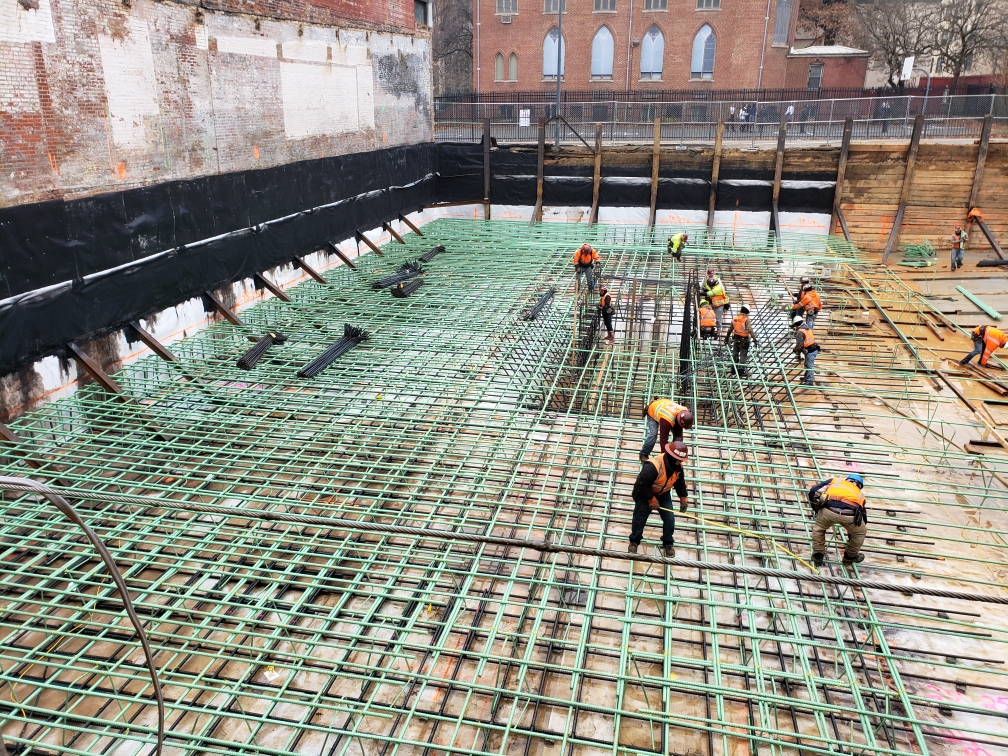
EPRO’s Geo-Seal systems are also resistant to damage caused by rainfall after installation. “One of the great advantages of using Geo-Seal 100 for this project was that the system could be subjected to rain after installation. The membrane was exposed to heavy rain and was not damaged or preactivated like traditional bentonite sheet membranes,” says Paul Conners, President of Conners Group.
With a strong track record providing solutions for complex sites, EPRO is expanding its presence in the Mid-Atlantic area by offering a suite of systems to address a variety of site conditions and project types.
Learn more about our Geo-Seal system and how it can help protect your next project, or start a no-obligation assessment.