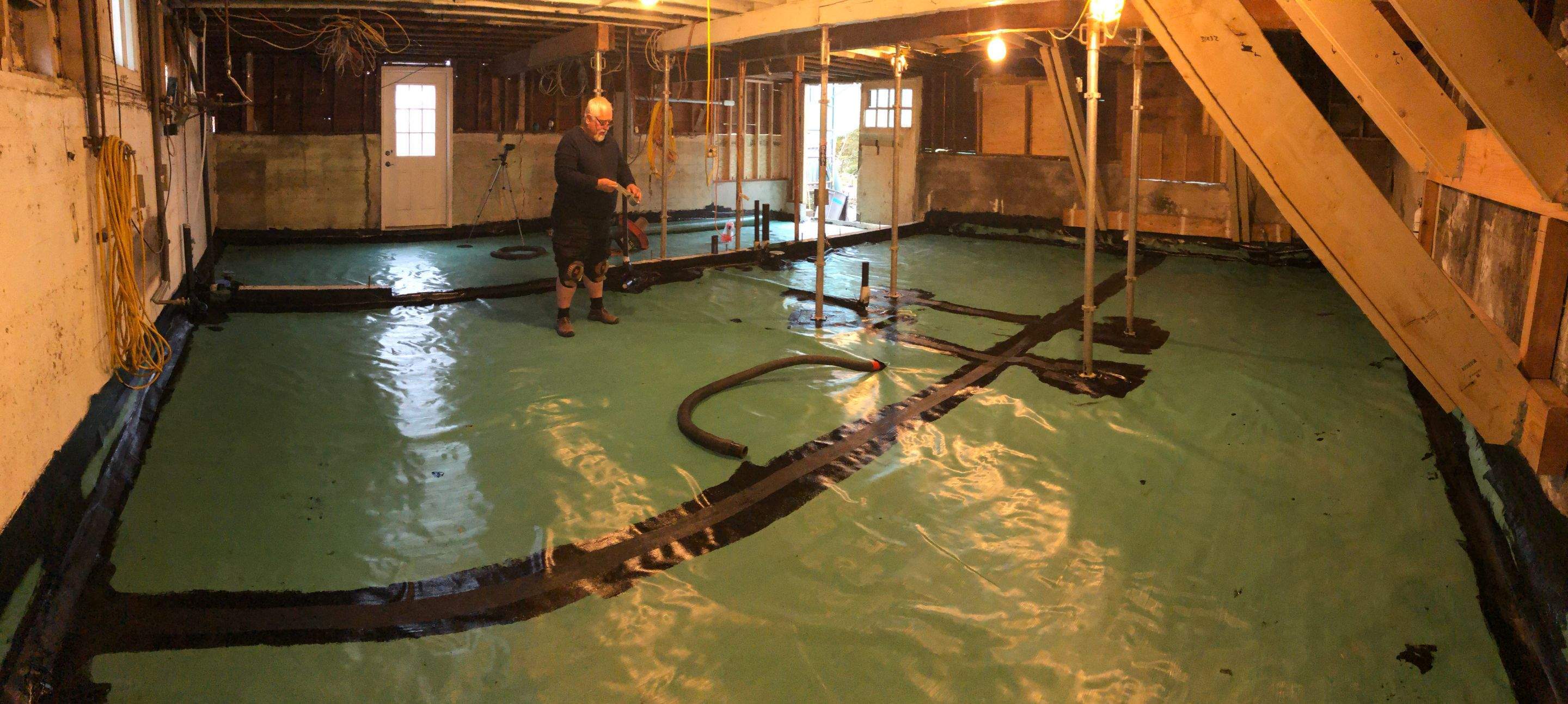
A private residence in the Ballard neighborhood of Seattle was purchased in 1991. The home had oil heating and a tank to store said oil; the tank was registered with the State of Washington’s “Heating Oil Pollution Liability Insurance Program,” which covers the cost up to $60,000 if it is necessary to clean up contamination.
The home was remodeled in 2021, and the plan included installing new electric heat pumps and removing the oil tank. Owners Marc Chavez, a Seattle-based specification writer, and Anne Harper hired a contractor to remove it, and they discovered the tank had been slowly leaking oil for many years. This meant that the soil below was contaminated, and after testing it was confirmed that a mitigation system would be needed to protect the residence.
The couple hired TechSolve Environmental, who specializes in soil and groundwater investigation, remediation, and mitigation of environmental liability. The existing basement slab, where the contamination was located, had been removed and a new one was planned to be placed at the same elevation. This new slab would also include a gravel sub-base, reinforcing, a below slab vapor barrier and insulation over the entire basement area. To accomplish this, approximately one foot of existing soil needed to be removed. Contaminated soils were hauled off to the appropriate licensed sites as preparation continued.
The contaminated soils went deeper than could be removed without undermining the house foundation. Complete removal of the soil was not economically feasible. Furthermore, an industry standard ASTM E 1745 Class A vapor retarder would not adequately contain the hydrocarbon vapors below the slab and keep the building safe.
EPRO was able to offer a below grade vapor intrusion solution that would fully protect the residence.
“This kind of work is usually preformed on commercial properties where large quantities of material are used and longer lead times are expected and scheduled for. Residential application is harder as there simply isn’t the network of suppliers and contractors to provide it,” says Chavez.
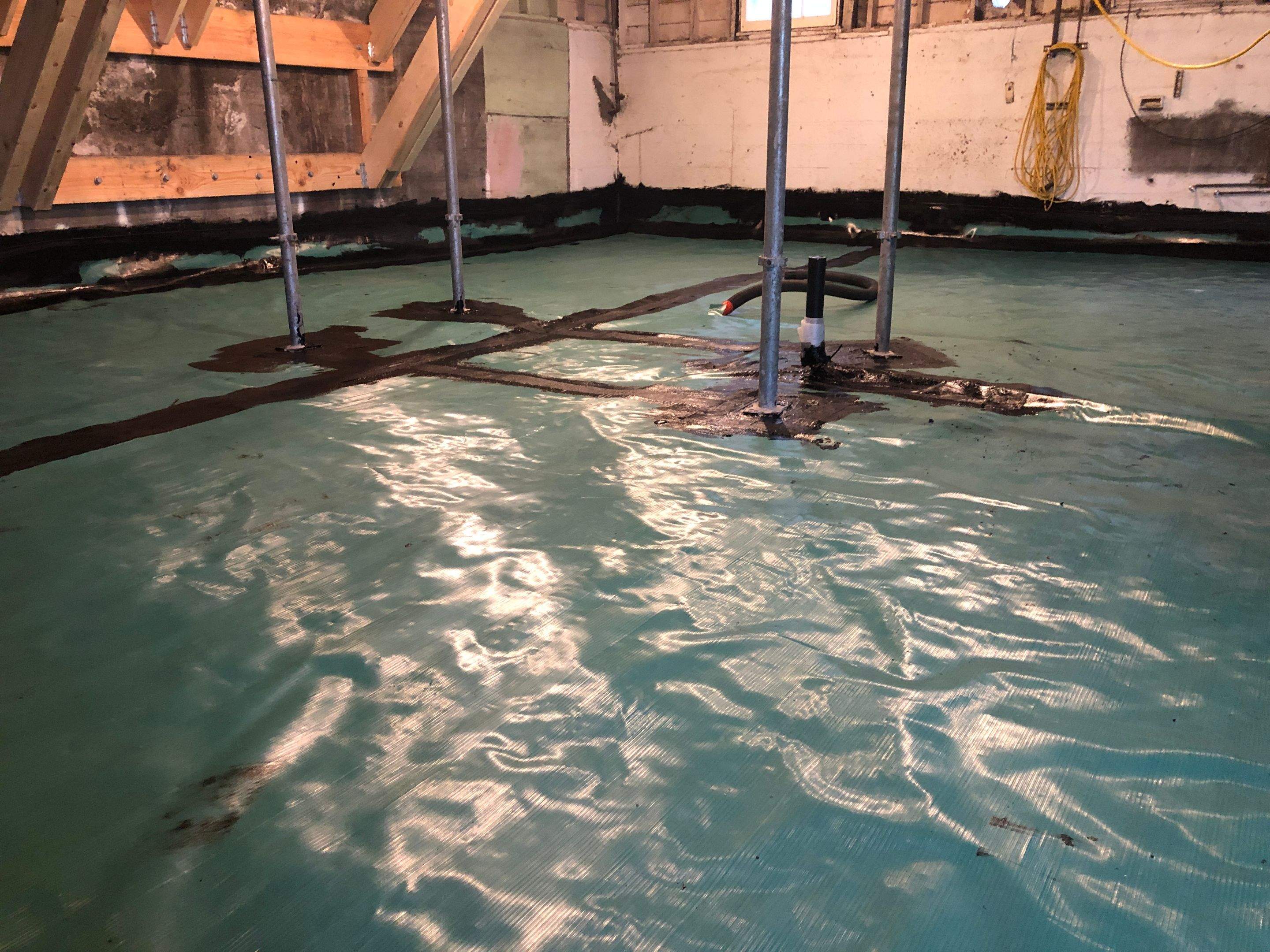
The contractor, Howe Interiors and Construction installed EPRO’s Geo-Seal vapor intrusion mitigation system. This solution was the easiest to install with the added benefit of having a “dry” layer on top that would allow the contractor to continue working in the basement without having to wait for material cure time.
“Howe Interiors and Construction, the contractor, noted no problems with installation,” says Chavez. “But the real ease was having a great product rep and having product available. It was extremely helpful that Mike could talk directly to the suppliers, see which products were in town and arrange for the small quantities we needed to be delivered on time.”
Geo-Seal is an innovative sub-slab vapor intrusion barrier system that eliminates vapor intrusion for brownfields or any environmentally-impaired site. Fully tested and proven highly effective against VOC vapors such as chlorinated solvents and petroleum hydrocarbons, as well as methane gas, Geo-Seal earns wide approval among various regulatory agencies.
Per standard EPRO protocol, a smoke test was performed to visually confirm that the system was sealed properly. Part of the process involves pumping smoke underneath the system to identify any areas that need to be repaired and once this is done, the system is signed off on and concrete is placed. The final step and initial vapor test revealed extremely low levels of vapor in the space, and further testing will confirm success of the finished basement later in 2023.
“I feel confident that we have contained everything,” adds Chavez.
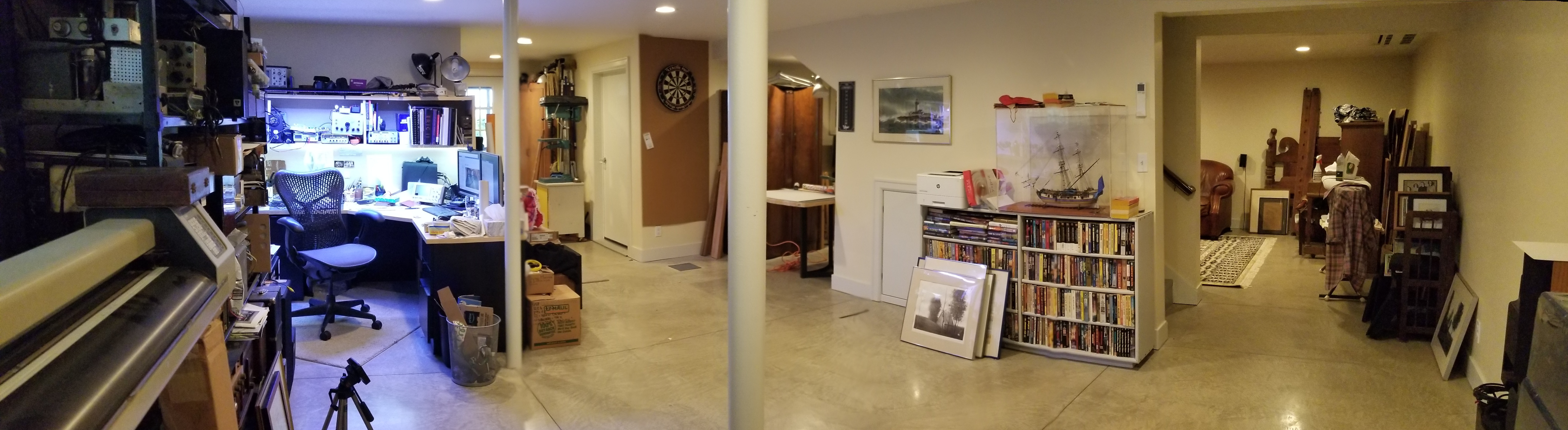